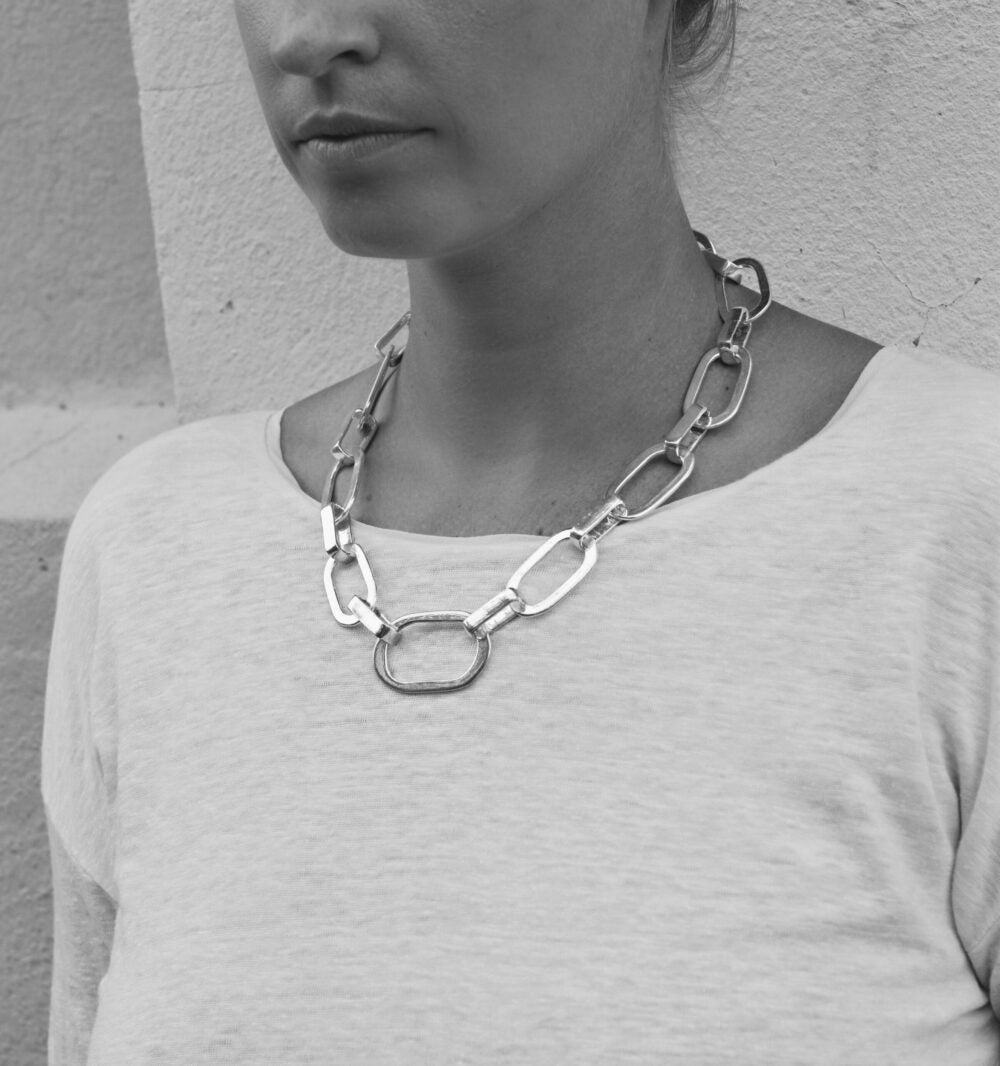
The Annie Necklace: A peek at my design (& re-design) process
A lot goes into each finished piece you see available here on our site, or at one of our retail partners. The design-focused trial and error process is what I love most about my business. It is where I feel the most creative and most excited, so I thought I would kick off our blog by giving you a peek at that process. This is the story - saga, really - of one of our best-sellers: The Annie Necklace
Chain has always fascinated me, especially chunky chain, the kind with substance that you can spot on someone from a distance. I even like the big spools of chain that you find in Lowes in all different sizes - some galvanized, some in yellow or black plastic. Recently, my daughter and I have begun a dream-project (I’ll talk more about this in an upcoming blog) that required us to clean out an old barn on our property. During that clean out process, I found a piece of really old chain broken & buried under the years. It was beautiful. I saved this chain. I photographed this chain. If you follow me on Instagram, you might have seen this chain - that’s how much I loved it. Chain always catches my eye.Â
One of the reasons I wanted to start carving wax & casting was to be able to make my own shapes that I could turn into custom chain links for necklaces and bracelets. I had been sketching and dreaming of making these links for a long time, and finally took some wax carving classes with Kate Wolf. She’s a badass wax carving guru located in Maine and I felt electric with ideas after those classes and workshops. The first substantial necklace I dreamed about was the Uma Necklace. It had 10 oval chain links anchored by a round disc in the center and joined together by silver sheet connectors that I fabricated and finished with a custom clasp.Â
As I said, it was substantial. I’m a tall woman and, as a lot of makers do, I often make jewelry to fit myself. However, for more petite women, these pieces can be overwhelming. I needed to redesign this necklace to fit someone with a smaller frame. Enter the Annie Necklace. My good friend Annie is a petite woman. Not afraid to wear a statement necklace, but petite none-the-less. I wanted to design something that could sit next to the Uma Necklace, but that she could wear comfortably day to day. I needed to make the links smaller and the overall feeling lighter. I kept the fabricated connectors and clasp the same. Perfect.Â
When I design a new piece, I always wear it for a while. Prototyping the pieces in this way ensures that they are wearable when they end up in a customer’s hands. It also helps me understand how to talk about the piece, because I have lived in it. I loved the Uma and I loved the Annie visually, but they just weren’t passing my comfort and wearability testing. When this happens, it always feels like a failure at first. I get so excited about the new piece and then...it’s a flop? Ugh. Back to the drawing board.
What wasn’t working? Why didn’t it feel right? The connecting pieces between the chunky new links were hindering fluid movement. They were stiff. It was as good a place to start as any... I needed to go back to the bench.Â
I carved a new connecting link to be cast which I hoped would give it more stability. It was a bear to carve - striking the balance between visual cohesion and lightweight wearability means getting the wax very thin...and the thinner the wax, the higher the risk that it crumbles in your hands.Â
When this link arrived back from the caster, I knew I had done it. It was perfect. I quickly put together a new Annie necklace with exclusively cast components and, although I wore it for a couple weeks to be sure, I knew instantly that it was now ready for customers to see and feel it. This process took months. There were so many ups and downs, so many moments that I wanted to say - it can’t be done - but ultimately it led me to a best-seller that is fully customizable based on height and an anchor for my cast collection.Â